The Occupational Safety and Health Administration (OSHA) provides detailed regulations regarding the use of personal protective equipment (PPE). The following information outlined by EHS is meant to help individuals understand those requirements and how to select the right PPE depending on the hazard, task, or location.
Assessing Your PPE Needs
When PPE is needed, regulations require that a hazard assessment be performed to identify the specific hazards of concern and the PPE required for protection from those hazards. This hazard assessment may be done for a work area, or for a specific experiment, job, or task. PPE is selected based on the hazard assessment.
Reach out to your Department, Lab, or Center’s (DLCI) EHS Coordinator for a PPE hazard assessment form and DLCI-specific PPE requirements, then use the information below to select appropriate PPE and clothing. DLCIs may choose to have groups use the basic PPE Hazard Assessment Form or the more comprehensive PPE Hazard Assessment Fillable Form to meet this requirement.
All individuals who use PPE must be provided specific training by their supervisor or area safety representatives about:
- Hazards
- PPE to be used
- Correct use and care of the PPE
- Limitations of the PPE
Using and Caring for Your PPE
Once appropriate PPE is determined, be sure it fits properly and you are trained on how to use and maintain it. Check reusable PPE both before and after use for damage. Do not use if damaged.
After use, reusable PPE should be cleaned if appropriate and stored in a manner that will keep it clean. Refer to the Guidelines for the Use and Disinfection of Shared PPE document for more details. Disposable PPE, especially gloves, should not be reused and must be disposed of in the appropriate waste stream.
Understanding the Limitations
PPE should not be used as a substitute for engineering controls such as fume hoods, glove boxes, biosafety cabinets, process enclosures, etc., or as a substitute for good work practices and personal hygiene. Conversely, use of engineering controls such as fume hoods does not preclude the need for wearing the proper PPE.
All PPE has limitations in terms of the type and magnitude of exposure they will protect against and this must also be taken into consideration during the hazard assessment process. Be sure to review any information related to the limitations of the specific PPE you are using.
Types of PPE
Wear appropriate clothing and PPE when in areas with hazards.
Table 1 summarizes the minimum PPE and clothing to be worn in most lab spaces. More detailed information on each type of PPE is found in the sections below. Note that specific labs or DLCIs may have stricter requirements. In some cases, through a hazard assessment, supervisors may identify situations (a task, experiment, or area) where alternative or more protective apparel must be worn.
The minimum required clothing and PPE outlined in the table is dependent on what an individual is doing in the lab. General categories include:
- Brief Lab Visit or Walk-through – This includes people that will only be in a lab space briefly, including but not limited to delivery personnel, MIT students and employees going through a space but not stopping to work, and tour participants. Visitors will not spend time observing or standing near areas where active work with chemicals, biologicals, radioactive materials, lasers, or other potential hazards are being used.
- Not Working With or Nearby to Chemicals, BL2 Materials, or Radioactive Materials – This includes but is not limited to those at desks or office areas within labs that are away from active work areas and those that are using equipment where there are no chemicals or other hazards.
- Working With or Nearby to Chemicals, BL2 Materials, or Radioactive Materials – This category includes those working with hazardous materials as well as those working nearby to those materials where there is an expected risk of exposure. People working at desks may fall under this category depending on the activities happening around the desk. Ultimately it is the responsibility of the PI to assess the hazards around desk areas and determine if lab coats or other PPE are required due to the proximity of hazardous materials or processes.
Non-lab areas, such as shops or Facilities work areas, have alternate requirements based on the types of hazards present.
Table 1: Selection of Lab PPE and Attire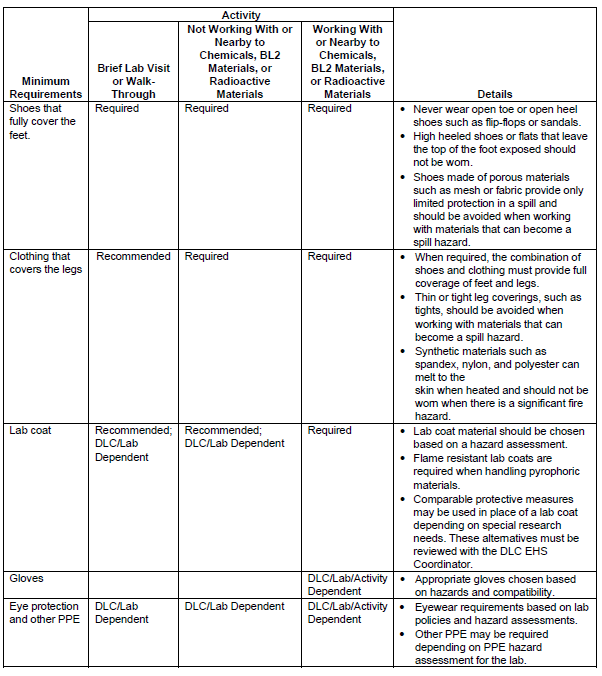
Click on the table to see a full PDF version.
Respiratory protection is used when other controls, such as fume hoods, are not able to reduce the potential level of inhalation exposure to an acceptable level. If you think you require a mask or some form of respiratory protection for your work, you must first contact EHS. We will help you determine if a respirator is required, what size and type would protect you best, and what type of filters/cartridges you should use.
OSHA Requirements
MIT’s Respiratory Protection Program has to abide by OSHA regulation 1910.134.
If you are required to use a respirator as protection against a hazardous material, then you must comply with all components of this law. Complete details are available at MIT’s Respiratory Protection Program.
Selection
The EHS Office will assist you in selecting the appropriate respirator when required based on the type of hazard(s) to be encountered. Note that respirators and beards don’t mix. Facial hair prevents a good seal between the respirator and your face, allowing chemicals to get in. If a person with a beard requires respiratory protection, contact EHS to discuss options such as PAPRs.
See the CDC facial hair respirator guide: https://blogs.cdc.gov/niosh-science-blog/2017/11/02/noshave/
Comfort (Voluntary) Mask and Respirator Use
If there is no health concern associated with your work, but you wish to wear a disposable dust mask to protect yourself from nuisance dust, fill out a voluntary use form available from EHS by contacting respirators@mit.edu.
If you wish to wear a reusable respirator to protect yourself from nuisance odors, please follow the instructions below on how to obtain a respirator.
Obtaining a Respirator
- Register for the Respiratory Program – Fill out the MIT Respirator Program Registration Form
- Fill out an Exposure Evaluation Form – A link to the Exposure Evaluation Form will be sent to you via email once you have completed Step 1 above. This form serves as a Hazard Assessment and helps to determine your need for respiratory protection.
- Complete a Medical Screening/Evaluation Form- Request a respirator medical clearance by contacting Occupational Health @ MIT Health through HealtheLife or by calling 617-253-8552.
MIT Health uses HealtheLife to securely transmit personal medical information because regular email is not secure. HealtheLife is a no-cost service available to anyone in the MIT community even if they are not a patient at MIT Health. If you do not have an account already, you can register for HealtheLife when you call and state you need Occupational Health services. Once contacted, Occupational Health will send a OSHA approved questionnaire for you to fill out and submit through HealtheLife. The OSHA questionnaire is used to determine if an in-person evaluation is required to clear you for respiratory protection; if so, you will be asked to make an appointment with Occupational Health. However, for many people, the questionnaire will be all that is needed; if so, you will be told that an appointment is not necessary. If you would prefer to go ahead and make an in-person appointment without filling out the questionnaire, please indicate this when you contact Occupational Health. (For example, anyone who uses a self-contained breathing apparatus must have an in-person evaluation. - Complete a Respirator Fit Test – Schedule a Fit Test (click here). NOTE: Successful competition of the medical clearance is a prerequisite to the fit test. The Industrial Hygiene Program conducts (quantitative) respirator fit tests at the EHS Office (Building N52-496). Each appointment typically takes approximately 10 minutes to complete. Once the initial respirator fit test has been completed a copy of the fit test record is sent to the respirator user along with this EHS Guide to care for your respirator that includes important information on proper use, storage, cleaning, etc. EHS has a small inventory of respirators and will provide a respirator and applicable cartridges. A chargeback will be applied to the lab group to cover the cost of the equipment.
Fit test training records are uploaded to the Atlas Learning Center on a monthly basis. - Annual requirements – EHS will send reminder emails when an annual respirator fit test is required or when a medical clearance has expired and needs to be renewed. Upon receiving the reminder email please complete the necessary requirements to remain in compliance with the OSHA 1910.134 or follow the instructions in the email to withdraw from the MIT Respiratory Protection Program.
Wear appropriate clothing when in laboratories, makerspaces and other areas with hazards.
A combination of clothing and shoes that fully cover the legs and feet is required when working in spaces that have hazardous chemicals, which includes almost all lab spaces. Similarly, there are requirements to have the legs covered in spaces with other hazards that could pose a risk to individuals, such as physical hazards or biological and radioactive materials that pose an exposure risk. Individuals briefly visiting a space are exempt from this requirement if they are not near hazardous materials.
Refer to Table 1. Selection of Lab PPE & Attire for additional recommendations on types of clothing and shoes to wear based on the hazards present.
Refer to the Protective Footwear section below for details on safety shoes.
Gloves can provide basic protection against hazards. Choose gloves that are clean and fit well and that are compatible and appropriate to the hazard being handled.
OSHA Requirements
OSHA requires use of appropriate hand protection when hands are exposed to hazards such as skin absorption of harmful substances, severe cuts or lacerations, severe abrasions, punctures, chemical burns, thermal burns, and harmful temperature extremes.
Additionally, for some jobs, the hands could become contaminated with work materials such as radioisotopes, biological agents, or chemicals. Gloves are often used to prevent hand contamination and to raise awareness regarding the potential for contamination of other surfaces touched by those gloves.
Glove Selection
When selecting gloves, be sure to understand the limitations of each glove type and material, and that a glove selected for protection against one type of hazard will not necessarily be effective against another type of hazard. If the work or task involves more than one type of hazard, this must be taken into consideration in selecting the best type or combination of gloves for the circumstances. Consideration should also be given to the level of dexterity required for a given activity.
In areas such as machine shops and work around rotating or moving machinery, gloves may create a hazard of being caught in the machinery and pulling the hand into the machine. As a general rule, don’t wear gloves around machinery such as lathes, table saws, and press drills unless the shop supervisor indicates otherwise. The specific task may determine if the use of gloves is feasible.
*Some people may be allergic to latex-containing materials. They should be offered other options for hand protection under these circumstances, e.g., nitrile or vinyl disposable gloves.
Table 2. Selection of Gloves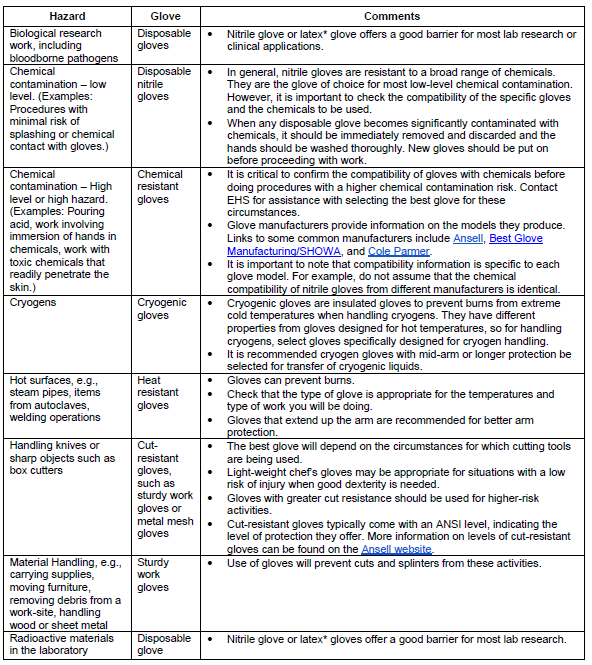
Click on the table for a full PDF version.
Clothing such as a lab coat, smock or coveralls may be used to provide protection from hazards that may damage the skin or personal clothing and can be used to protect an individual’s personal clothing from contamination or dirt that can be carried home or to other areas. The lab coat is to be worn in the lab and removed when the individual leaves the laboratory space.
Visit MIT’s website dedicated to lab coats for additional information.
MIT Policy on Lab Coats
MIT’s policy on lab coats, as set by the MIT Committee on Toxic Chemicals, states:
“A laboratory coat or equivalent protection is required when working with or when working nearby to hazardous chemicals, unsealed radioactive materials, and biological agents at BL2 or greater. A flame-resistant lab coat is required when handling pyrophoric substances outside of a glove box. It is recommended that a flame-resistant lab coat be worn when working with all flammable chemicals. Laboratory supervisors shall carry out a hazard assessment to identify situations (a task, experiment, or area) where alternative or more protective apparel must be worn.”
This policy means that most people working in a lab must wear a lab coat or equivalent, for some, if not all the work they do. In some cases, your DLCI or lab may have more restrictive rules regarding the appropriate use of lab coats.
Refer to the information above regarding the assessment process.
Lab Coat Selection
There are many types of lab coats. The most common are polyester/cotton lab coats for low-risk lab work, flame resistant (FR) lab coats for pyrophorics and other fire hazards, and chemical resistant (CP) lab coats for work where there is a higher chemical exposure risk, particularly from corrosives. For more information on the use and selection of lab coats review the Lab Coat Guidance.
Obtaining Lab Coats
For questions regarding lab coat supply and laundry services available, see the Lab Coat FAQs.
Caring For Lab Coats
While disposable clothing should be thrown away after use, arrangements should be made to ensure reusable PPE such as reusable lab coats or coveralls is cleaned at work or by a service.
People must not take potentially contaminated PPE, such as lab coats, home for cleaning. For laundry service options for lab coats, review the Lab Coat Guidance.
In some cases, other protective gear should be used with or instead of lab coats. Examples include the following.
Alternative Protective Gear
Rubber Apron or Chemical Resistant Suit
A rubber apron or a chemical-resistant suit may be needed for work with corrosive chemicals, depending on the specific task to be done.
Coveralls
Coveralls can be used to protect a maintenance employee’s skin and clothing from contamination in dirty areas or from high levels of dust generated during some jobs.
Smocks
Smocks can be used for the protection of skin and clothing during cleaning or other activities.
Damage to the eyes and loss of sight is irreversible, so it is important to identify potential eye hazards, select proper eye protection, and enforce its use. Eye protection is required by OSHA regulation whenever and wherever potential eye hazards exist. Hazards requiring eye and/or face protection include flying particles, molten metal, liquids including acids or caustic materials, biological or radioactive materials, chemical gases or vapors, and potentially injurious light radiation such as lasers or intense visible light from welding. Note that even very small amounts of a material may cause eye damage and require use of protective eyewear.
Selection of Eye and Face Protection
For laboratory areas, PIs are required to be involved in the hazard assessment process for eye protection use unless eye protection is required for entry into the lab area. Contact your DLCI EHS Coordinator or the EHS Office for assistance.
Types of protective eyewear include:
- Safety glasses with side shields (built-in or clip-on)
- Goggles for chemical splash or mist (indirect vents)
- Goggles for chips or dust (direct vents)
- Face shield when there is a higher risk of splashes or flying materials – Must be worn with goggles to prevent liquid chemicals from getting into the eyes. Must be worn with safety glasses to prevent chips or other particles from getting into the eyes.
Table 3. Selection of Eye and Face Protection outlines common hazards and the typical eye and face protection used. Contact your DLCI EHS Coordinator or refer to the EHS Website to identify the point person from each EHS specialty listed for your DLCI.
Table 3. Selection of Eye and Face Protection
Click on the table to see full PDF version.
Note 1: Prescription safety glasses can be obtained through the MIT Optical Shop. Details are below. Note that if you need to wear a full-face respirator and prescription glasses you can order prescription lenses that fit into the respirator through IHP.
Note 2: Prescription safety glasses can be made with lenses designed for working with lasers, or alternatively you could purchase a pair of laser safety glasses that can be worn over prescription glasses.
Note 3: If you need to wear welding goggles, a helmet or face shield in addition to prescription glasses, you can order prescription lenses that fit into the filter shade lenses.
Labs can contact the EHS Office for additional guidance on selecting the correct type of eye protection.
Obtaining Eyewear
DLCIs are responsible for providing appropriate protection to anyone who works in, studies in or visits an area where there are hazards to the eyes and/or face.
Eye protection provided must meet the American National Standards Institute standard or equivalent (ANSI Z87.1). Normal prescription glasses do not meet the standard for impact resistance and should not be used as a substitute for safety glasses.
Non-Prescription Eyewear
VWR and many other safety supply companies sell a wide variety of non-prescription glasses, goggles, etc. Check that the eyewear meets the ANSI Z87.1 standard or equivalent.
Ordering Prescription Safety Glasses
DLCIs must furnish one pair of prescription impact-resistant (ANSI Z87) eyeglasses free of charge to employees and/or students whose work requires their use. The supervisor must approve all requests for prescription safety glasses. Please visit the MIT Health Optical Shop for detailed information on how to get prescription safety glasses and refer to the pricing sheet.
Undergraduate students who don’t have DLCI funding can pay for their glasses directly and don’t need a supervisor to sign the form.
If your glasses break, are scratched or your prescription changes, then order a new pair by following the procedure on the Optical Shop and the DLCI will pay for the new glasses. You will only need to pay for the new prescription if it has changed or if it is more than 2 years old. Bifocal and Base progressive lenses will be furnished when necessary.
Use
Wear eye protection in areas where it is required, whether you are working, observing, or visiting. Also wear in areas or for tasks where you have been instructed eye protection is to be used.
In some circumstances safety glasses or goggles alone may not provide adequate protection; a face shield may also be necessary.
Caring for Eyewear
Clean eye protection after use and store where it can be kept clean until next use. Do not leave it on work benches or other areas where there is a contamination risk.
Additional Info and Resources
Refer to PPE SOP (certificate required) for more details on eye protection.
Some tasks or work environments have hazards that could cause foot damage. Consider the potential risks to the feet and choose footwear accordingly.
OSHA Requirements
OSHA requires use of protective footwear when working in areas where foot injuries could occur due to falling or rolling objects, objects piercing the sole, or exposure to electrical hazards. In addition to OSHA, there may be other circumstances where use of protective footwear (safety shoes) is advisable, for example, use of rubber boots when working in flooded areas or areas contaminated with sewage.
Selection of Protective Footwear
Identify the hazards through a hazard assessment (details above), then use this information to determine if protective footwear is required and, if yes, what type of footwear is needed. Supervisors will inform personnel if safety shoes are needed for a job, and what type of safety shoes. Safety shoes must meet the requirements of ASTM F2413-2018, which requires 3rd party certification.
The following outlines the procedure to follow for Facilities, CAC, Housing, and DCM employees. People in other DLCIs should check with their supervisor or DLCI EHS Coordinator for assistance.
- If a job requires hard toed safety shoes, the Supervisor will notify the individual.
- The employee checks that the shoes meet the ASTM F2413-(date) standard before purchasing. The year that the standard was updated may be listed after ASTM F2413. This means that the shoes have “steel toes” and the ASTM F2413-(date)stamp, which is usually on the shoe’s tongue or on the side near the heel. Sometimes this is on an attached tag/band.
- If the ASTM F2413-(date) number is not on the shoes, then the shoes do not meet the ASTM F2413-(date) standard and MIT will not reimburse the employee.
- The employee brings their new shoes to their Supervisor, who will check the shoes for the ASTM F2413-(date) stamp. Reminder: Do not wear the shoes until after you have received this approval.
- The Supervisor will sign a safety shoe card or equivalent.
- The Supervisor or employee takes the signed shoe card and the original store receipt to their department to be reimbursed. Copies of the receipt or credit card statement will not be accepted but the employee should keep a copy since you will not get the original receipt back. The department will check the employee’s balance and when they were last reimbursed. The department will reimburse the employee for the amount allowed per the union contract, if applicable. The EHS Office does not provide this reimbursement.
- Jani Findlay in E18-102 (x3-6381) processes the reimbursements for Department of Facilities and CAC. The reimbursement is posted directly into the bank account that the person’s payroll is deposited into.
- Scott Fleming in W20-507 (x3-0967) reimburses Housing employees, who sign to document the payment.
- Lesley Fowler in 16-849 (x5-4810) reimburses employees in the Division of Comparative Medicine. The employee signs to document the payment.
- All other DLCI’s: contact your DLCI headquarters office about the procedure.
- The department will be responsible for keeping records for the duration of the employment. The department will keep the original receipts until the employee obtains another pair. (Receipts do not need to be sent to the EHS Office.)
- The Supervisor will periodically check that the employee is wearing the safety shoes when performing tasks that could result in a foot injury. If the employee is not wearing their safety shoes, the Supervisor will ask the employee to put the shoes on and will document this. If the employee has an accident but the employee was not wearing their safety shoes, the claim could be denied. The department will be asked for their records, including safety shoe purchases.
Hearing protection, such as earplugs or earmuffs, is required at MIT in areas where individuals may be exposed to noise at or above the MIT action level of 82 dBA as a time-weighted average over 8 hours or where the maximum sound level is at or above 140 dBC or dBZ. More information can be found on the Hearing Conservation webpage and in the Hearing Conservation Program SOP (certificate required).
Additional Resources
- PPE SOP (certificate login required; Forms & SOPs – Filter by – Keyword: PPE)
- Lab Coat Website
- Fact Sheets
The Occupational Safety and Health Administration (OSHA) provides detailed regulations regarding the use of personal protective equipment (PPE). The following information outlined by EHS is meant to help individuals understand those requirements and how to select the right PPE depending on the hazard, task, or location.
Assessing Your PPE Needs
When PPE is needed, regulations require that a hazard assessment be performed to identify the specific hazards of concern and the PPE required for protection from those hazards. This hazard assessment may be done for a work area, or for a specific experiment, job, or task. PPE is selected based on the hazard assessment.
Reach out to your Department, Lab, or Center’s (DLCI) EHS Coordinator for a PPE hazard assessment form and DLCI-specific PPE requirements, then use the information below to select appropriate PPE and clothing. DLCIs may choose to have groups use the basic PPE Hazard Assessment Form or the more comprehensive PPE Hazard Assessment Fillable Form to meet this requirement.
All individuals who use PPE must be provided specific training by their supervisor or area safety representatives about:
- Hazards
- PPE to be used
- Correct use and care of the PPE
- Limitations of the PPE
Using and Caring for Your PPE
Once appropriate PPE is determined, be sure it fits properly and you are trained on how to use and maintain it. Check reusable PPE both before and after use for damage. Do not use if damaged.
After use, reusable PPE should be cleaned if appropriate and stored in a manner that will keep it clean. Refer to the Guidelines for the Use and Disinfection of Shared PPE document for more details. Disposable PPE, especially gloves, should not be reused and must be disposed of in the appropriate waste stream.
Understanding the Limitations
PPE should not be used as a substitute for engineering controls such as fume hoods, glove boxes, biosafety cabinets, process enclosures, etc., or as a substitute for good work practices and personal hygiene. Conversely, use of engineering controls such as fume hoods does not preclude the need for wearing the proper PPE.
All PPE has limitations in terms of the type and magnitude of exposure they will protect against and this must also be taken into consideration during the hazard assessment process. Be sure to review any information related to the limitations of the specific PPE you are using.
Types of PPE
Wear appropriate clothing and PPE when in areas with hazards.
Table 1 summarizes the minimum PPE and clothing to be worn in most lab spaces. More detailed information on each type of PPE is found in the sections below. Note that specific labs or DLCIs may have stricter requirements. In some cases, through a hazard assessment, supervisors may identify situations (a task, experiment, or area) where alternative or more protective apparel must be worn.
The minimum required clothing and PPE outlined in the table is dependent on what an individual is doing in the lab. General categories include:
- Brief Lab Visit or Walk-through – This includes people that will only be in a lab space briefly, including but not limited to delivery personnel, MIT students and employees going through a space but not stopping to work, and tour participants. Visitors will not spend time observing or standing near areas where active work with chemicals, biologicals, radioactive materials, lasers, or other potential hazards are being used.
- Not Working With or Nearby to Chemicals, BL2 Materials, or Radioactive Materials – This includes but is not limited to those at desks or office areas within labs that are away from active work areas and those that are using equipment where there are no chemicals or other hazards.
- Working With or Nearby to Chemicals, BL2 Materials, or Radioactive Materials – This category includes those working with hazardous materials as well as those working nearby to those materials where there is an expected risk of exposure. People working at desks may fall under this category depending on the activities happening around the desk. Ultimately it is the responsibility of the PI to assess the hazards around desk areas and determine if lab coats or other PPE are required due to the proximity of hazardous materials or processes.
Non-lab areas, such as shops or Facilities work areas, have alternate requirements based on the types of hazards present.
Table 1: Selection of Lab PPE and Attire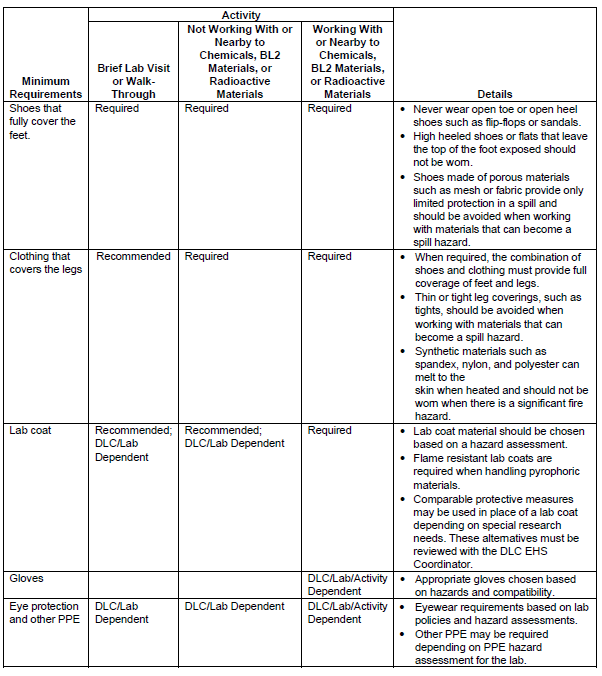
Click on the table to see a full PDF version.
Respiratory protection is used when other controls, such as fume hoods, are not able to reduce the potential level of inhalation exposure to an acceptable level. If you think you require a mask or some form of respiratory protection for your work, you must first contact EHS. We will help you determine if a respirator is required, what size and type would protect you best, and what type of filters/cartridges you should use.
OSHA Requirements
MIT’s Respiratory Protection Program has to abide by OSHA regulation 1910.134.
If you are required to use a respirator as protection against a hazardous material, then you must comply with all components of this law. Complete details are available at MIT’s Respiratory Protection Program.
Selection
The EHS Office will assist you in selecting the appropriate respirator when required based on the type of hazard(s) to be encountered. Note that respirators and beards don’t mix. Facial hair prevents a good seal between the respirator and your face, allowing chemicals to get in. If a person with a beard requires respiratory protection, contact EHS to discuss options such as PAPRs.
See the CDC facial hair respirator guide: https://blogs.cdc.gov/niosh-science-blog/2017/11/02/noshave/
Comfort (Voluntary) Mask and Respirator Use
If there is no health concern associated with your work, but you wish to wear a disposable dust mask to protect yourself from nuisance dust, fill out a voluntary use form available from EHS by contacting respirators@mit.edu.
If you wish to wear a reusable respirator to protect yourself from nuisance odors, please follow the instructions below on how to obtain a respirator.
Obtaining a Respirator
- Register for the Respiratory Program – Fill out the MIT Respirator Program Registration Form
- Fill out an Exposure Evaluation Form – A link to the Exposure Evaluation Form will be sent to you via email once you have completed Step 1 above. This form serves as a Hazard Assessment and helps to determine your need for respiratory protection.
- Complete a Medical Screening/Evaluation Form- Request a respirator medical clearance by contacting Occupational Health @ MIT Health through HealtheLife or by calling 617-253-8552.
MIT Health uses HealtheLife to securely transmit personal medical information because regular email is not secure. HealtheLife is a no-cost service available to anyone in the MIT community even if they are not a patient at MIT Health. If you do not have an account already, you can register for HealtheLife when you call and state you need Occupational Health services. Once contacted, Occupational Health will send a OSHA approved questionnaire for you to fill out and submit through HealtheLife. The OSHA questionnaire is used to determine if an in-person evaluation is required to clear you for respiratory protection; if so, you will be asked to make an appointment with Occupational Health. However, for many people, the questionnaire will be all that is needed; if so, you will be told that an appointment is not necessary. If you would prefer to go ahead and make an in-person appointment without filling out the questionnaire, please indicate this when you contact Occupational Health. (For example, anyone who uses a self-contained breathing apparatus must have an in-person evaluation. - Complete a Respirator Fit Test – Schedule a Fit Test (click here). NOTE: Successful competition of the medical clearance is a prerequisite to the fit test. The Industrial Hygiene Program conducts (quantitative) respirator fit tests at the EHS Office (Building N52-496). Each appointment typically takes approximately 10 minutes to complete. Once the initial respirator fit test has been completed a copy of the fit test record is sent to the respirator user along with this EHS Guide to care for your respirator that includes important information on proper use, storage, cleaning, etc. EHS has a small inventory of respirators and will provide a respirator and applicable cartridges. A chargeback will be applied to the lab group to cover the cost of the equipment.
Fit test training records are uploaded to the Atlas Learning Center on a monthly basis. - Annual requirements – EHS will send reminder emails when an annual respirator fit test is required or when a medical clearance has expired and needs to be renewed. Upon receiving the reminder email please complete the necessary requirements to remain in compliance with the OSHA 1910.134 or follow the instructions in the email to withdraw from the MIT Respiratory Protection Program.
Wear appropriate clothing when in laboratories, makerspaces and other areas with hazards.
A combination of clothing and shoes that fully cover the legs and feet is required when working in spaces that have hazardous chemicals, which includes almost all lab spaces. Similarly, there are requirements to have the legs covered in spaces with other hazards that could pose a risk to individuals, such as physical hazards or biological and radioactive materials that pose an exposure risk. Individuals briefly visiting a space are exempt from this requirement if they are not near hazardous materials.
Refer to Table 1. Selection of Lab PPE & Attire for additional recommendations on types of clothing and shoes to wear based on the hazards present.
Refer to the Protective Footwear section below for details on safety shoes.
Gloves can provide basic protection against hazards. Choose gloves that are clean and fit well and that are compatible and appropriate to the hazard being handled.
OSHA Requirements
OSHA requires use of appropriate hand protection when hands are exposed to hazards such as skin absorption of harmful substances, severe cuts or lacerations, severe abrasions, punctures, chemical burns, thermal burns, and harmful temperature extremes.
Additionally, for some jobs, the hands could become contaminated with work materials such as radioisotopes, biological agents, or chemicals. Gloves are often used to prevent hand contamination and to raise awareness regarding the potential for contamination of other surfaces touched by those gloves.
Glove Selection
When selecting gloves, be sure to understand the limitations of each glove type and material, and that a glove selected for protection against one type of hazard will not necessarily be effective against another type of hazard. If the work or task involves more than one type of hazard, this must be taken into consideration in selecting the best type or combination of gloves for the circumstances. Consideration should also be given to the level of dexterity required for a given activity.
In areas such as machine shops and work around rotating or moving machinery, gloves may create a hazard of being caught in the machinery and pulling the hand into the machine. As a general rule, don’t wear gloves around machinery such as lathes, table saws, and press drills unless the shop supervisor indicates otherwise. The specific task may determine if the use of gloves is feasible.
*Some people may be allergic to latex-containing materials. They should be offered other options for hand protection under these circumstances, e.g., nitrile or vinyl disposable gloves.
Table 2. Selection of Gloves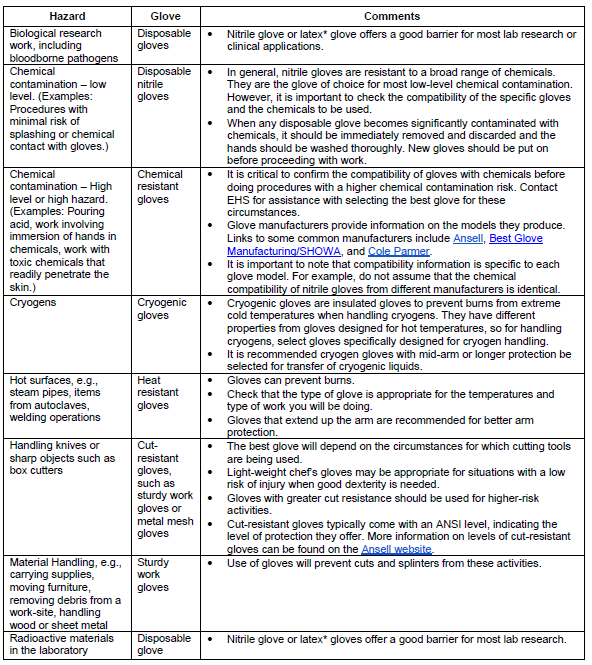
Click on the table for a full PDF version.
Clothing such as a lab coat, smock or coveralls may be used to provide protection from hazards that may damage the skin or personal clothing and can be used to protect an individual’s personal clothing from contamination or dirt that can be carried home or to other areas. The lab coat is to be worn in the lab and removed when the individual leaves the laboratory space.
Visit MIT’s website dedicated to lab coats for additional information.
MIT Policy on Lab Coats
MIT’s policy on lab coats, as set by the MIT Committee on Toxic Chemicals, states:
“A laboratory coat or equivalent protection is required when working with or when working nearby to hazardous chemicals, unsealed radioactive materials, and biological agents at BL2 or greater. A flame-resistant lab coat is required when handling pyrophoric substances outside of a glove box. It is recommended that a flame-resistant lab coat be worn when working with all flammable chemicals. Laboratory supervisors shall carry out a hazard assessment to identify situations (a task, experiment, or area) where alternative or more protective apparel must be worn.”
This policy means that most people working in a lab must wear a lab coat or equivalent, for some, if not all the work they do. In some cases, your DLCI or lab may have more restrictive rules regarding the appropriate use of lab coats.
Refer to the information above regarding the assessment process.
Lab Coat Selection
There are many types of lab coats. The most common are polyester/cotton lab coats for low-risk lab work, flame resistant (FR) lab coats for pyrophorics and other fire hazards, and chemical resistant (CP) lab coats for work where there is a higher chemical exposure risk, particularly from corrosives. For more information on the use and selection of lab coats review the Lab Coat Guidance.
Obtaining Lab Coats
For questions regarding lab coat supply and laundry services available, see the Lab Coat FAQs.
Caring For Lab Coats
While disposable clothing should be thrown away after use, arrangements should be made to ensure reusable PPE such as reusable lab coats or coveralls is cleaned at work or by a service.
People must not take potentially contaminated PPE, such as lab coats, home for cleaning. For laundry service options for lab coats, review the Lab Coat Guidance.
In some cases, other protective gear should be used with or instead of lab coats. Examples include the following.
Alternative Protective Gear
Rubber Apron or Chemical Resistant Suit
A rubber apron or a chemical-resistant suit may be needed for work with corrosive chemicals, depending on the specific task to be done.
Coveralls
Coveralls can be used to protect a maintenance employee’s skin and clothing from contamination in dirty areas or from high levels of dust generated during some jobs.
Smocks
Smocks can be used for the protection of skin and clothing during cleaning or other activities.
Damage to the eyes and loss of sight is irreversible, so it is important to identify potential eye hazards, select proper eye protection, and enforce its use. Eye protection is required by OSHA regulation whenever and wherever potential eye hazards exist. Hazards requiring eye and/or face protection include flying particles, molten metal, liquids including acids or caustic materials, biological or radioactive materials, chemical gases or vapors, and potentially injurious light radiation such as lasers or intense visible light from welding. Note that even very small amounts of a material may cause eye damage and require use of protective eyewear.
Selection of Eye and Face Protection
For laboratory areas, PIs are required to be involved in the hazard assessment process for eye protection use unless eye protection is required for entry into the lab area. Contact your DLCI EHS Coordinator or the EHS Office for assistance.
Types of protective eyewear include:
- Safety glasses with side shields (built-in or clip-on)
- Goggles for chemical splash or mist (indirect vents)
- Goggles for chips or dust (direct vents)
- Face shield when there is a higher risk of splashes or flying materials – Must be worn with goggles to prevent liquid chemicals from getting into the eyes. Must be worn with safety glasses to prevent chips or other particles from getting into the eyes.
Table 3. Selection of Eye and Face Protection outlines common hazards and the typical eye and face protection used. Contact your DLCI EHS Coordinator or refer to the EHS Website to identify the point person from each EHS specialty listed for your DLCI.
Table 3. Selection of Eye and Face Protection
Click on the table to see full PDF version.
Note 1: Prescription safety glasses can be obtained through the MIT Optical Shop. Details are below. Note that if you need to wear a full-face respirator and prescription glasses you can order prescription lenses that fit into the respirator through IHP.
Note 2: Prescription safety glasses can be made with lenses designed for working with lasers, or alternatively you could purchase a pair of laser safety glasses that can be worn over prescription glasses.
Note 3: If you need to wear welding goggles, a helmet or face shield in addition to prescription glasses, you can order prescription lenses that fit into the filter shade lenses.
Labs can contact the EHS Office for additional guidance on selecting the correct type of eye protection.
Obtaining Eyewear
DLCIs are responsible for providing appropriate protection to anyone who works in, studies in or visits an area where there are hazards to the eyes and/or face.
Eye protection provided must meet the American National Standards Institute standard or equivalent (ANSI Z87.1). Normal prescription glasses do not meet the standard for impact resistance and should not be used as a substitute for safety glasses.
Non-Prescription Eyewear
VWR and many other safety supply companies sell a wide variety of non-prescription glasses, goggles, etc. Check that the eyewear meets the ANSI Z87.1 standard or equivalent.
Ordering Prescription Safety Glasses
DLCIs must furnish one pair of prescription impact-resistant (ANSI Z87) eyeglasses free of charge to employees and/or students whose work requires their use. The supervisor must approve all requests for prescription safety glasses. Please visit the MIT Health Optical Shop for detailed information on how to get prescription safety glasses and refer to the pricing sheet.
Undergraduate students who don’t have DLCI funding can pay for their glasses directly and don’t need a supervisor to sign the form.
If your glasses break, are scratched or your prescription changes, then order a new pair by following the procedure on the Optical Shop and the DLCI will pay for the new glasses. You will only need to pay for the new prescription if it has changed or if it is more than 2 years old. Bifocal and Base progressive lenses will be furnished when necessary.
Use
Wear eye protection in areas where it is required, whether you are working, observing, or visiting. Also wear in areas or for tasks where you have been instructed eye protection is to be used.
In some circumstances safety glasses or goggles alone may not provide adequate protection; a face shield may also be necessary.
Caring for Eyewear
Clean eye protection after use and store where it can be kept clean until next use. Do not leave it on work benches or other areas where there is a contamination risk.
Additional Info and Resources
Refer to PPE SOP (certificate required) for more details on eye protection.
Some tasks or work environments have hazards that could cause foot damage. Consider the potential risks to the feet and choose footwear accordingly.
OSHA Requirements
OSHA requires use of protective footwear when working in areas where foot injuries could occur due to falling or rolling objects, objects piercing the sole, or exposure to electrical hazards. In addition to OSHA, there may be other circumstances where use of protective footwear (safety shoes) is advisable, for example, use of rubber boots when working in flooded areas or areas contaminated with sewage.
Selection of Protective Footwear
Identify the hazards through a hazard assessment (details above), then use this information to determine if protective footwear is required and, if yes, what type of footwear is needed. Supervisors will inform personnel if safety shoes are needed for a job, and what type of safety shoes. Safety shoes must meet the requirements of ASTM F2413-2018, which requires 3rd party certification.
The following outlines the procedure to follow for Facilities, CAC, Housing, and DCM employees. People in other DLCIs should check with their supervisor or DLCI EHS Coordinator for assistance.
- If a job requires hard toed safety shoes, the Supervisor will notify the individual.
- The employee checks that the shoes meet the ASTM F2413-(date) standard before purchasing. The year that the standard was updated may be listed after ASTM F2413. This means that the shoes have “steel toes” and the ASTM F2413-(date)stamp, which is usually on the shoe’s tongue or on the side near the heel. Sometimes this is on an attached tag/band.
- If the ASTM F2413-(date) number is not on the shoes, then the shoes do not meet the ASTM F2413-(date) standard and MIT will not reimburse the employee.
- The employee brings their new shoes to their Supervisor, who will check the shoes for the ASTM F2413-(date) stamp. Reminder: Do not wear the shoes until after you have received this approval.
- The Supervisor will sign a safety shoe card or equivalent.
- The Supervisor or employee takes the signed shoe card and the original store receipt to their department to be reimbursed. Copies of the receipt or credit card statement will not be accepted but the employee should keep a copy since you will not get the original receipt back. The department will check the employee’s balance and when they were last reimbursed. The department will reimburse the employee for the amount allowed per the union contract, if applicable. The EHS Office does not provide this reimbursement.
- Jani Findlay in E18-102 (x3-6381) processes the reimbursements for Department of Facilities and CAC. The reimbursement is posted directly into the bank account that the person’s payroll is deposited into.
- Scott Fleming in W20-507 (x3-0967) reimburses Housing employees, who sign to document the payment.
- Lesley Fowler in 16-849 (x5-4810) reimburses employees in the Division of Comparative Medicine. The employee signs to document the payment.
- All other DLCI’s: contact your DLCI headquarters office about the procedure.
- The department will be responsible for keeping records for the duration of the employment. The department will keep the original receipts until the employee obtains another pair. (Receipts do not need to be sent to the EHS Office.)
- The Supervisor will periodically check that the employee is wearing the safety shoes when performing tasks that could result in a foot injury. If the employee is not wearing their safety shoes, the Supervisor will ask the employee to put the shoes on and will document this. If the employee has an accident but the employee was not wearing their safety shoes, the claim could be denied. The department will be asked for their records, including safety shoe purchases.
Hearing protection, such as earplugs or earmuffs, is required at MIT in areas where individuals may be exposed to noise at or above the MIT action level of 82 dBA as a time-weighted average over 8 hours or where the maximum sound level is at or above 140 dBC or dBZ. More information can be found on the Hearing Conservation webpage and in the Hearing Conservation Program SOP (certificate required).
Additional Resources
- PPE SOP (certificate login required; Forms & SOPs – Filter by – Keyword: PPE)
- Lab Coat Website
- Fact Sheets